Sun-fired ceramics — A day with the pottery makers in Paphos
by Isabelle Martens
1. Dawn clay in Geroskipou
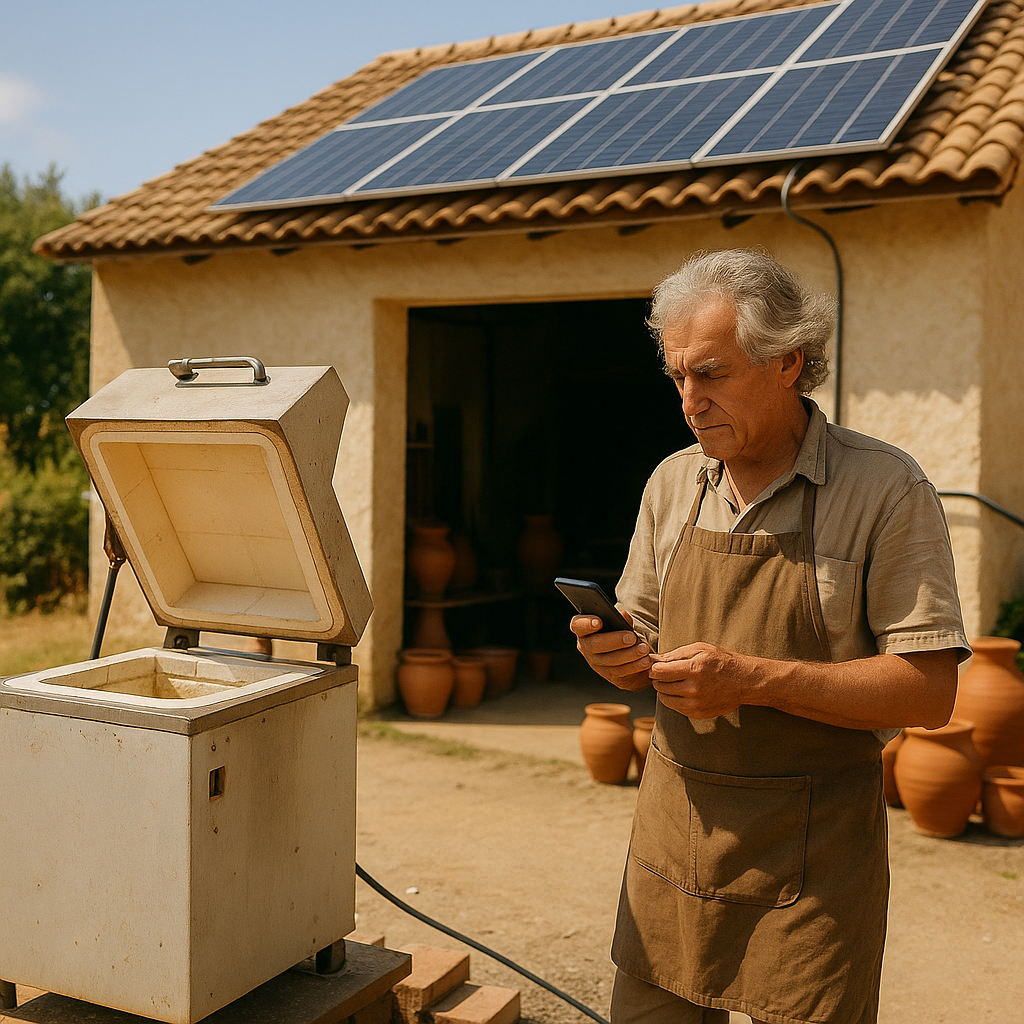
It's still cool when I roll into the courtyard of Avgoustinos Pottery. Avgoustinos himself — silver-locked hair, hands that remember forty years of pottery wheels — greets with a steaming coffee cup. "The clay gets to wake up before the sun does," he smiles and shows a raw earth sample: reddish-brown powder from Ezousa valley riverbeds, rich in iron and calcium, exactly the blend used in Hellenistic amphorae according to archaeologists.
When the wheel's first revolution spins, the coarse-grained lump softens between my palms; the scent is like wet terrace after summer rain. Avgoustinos points toward the open gate: "Today the sun will do the heavy lifting."
2. A kiln driven by the sky
Behind the workshop stands a newly built chamber in refractory brick, connected to a battery pack and 18 photovoltaic panels on the roof. The system is "solar-ready": a standard electric kiln that lets the PV installation feed kilowatt-hours directly into the firing circuit.
– How far do the panels reach?
– "A full bisque firing to 950°C takes about 80 kWh," he answers and shows yesterday's log on his phone where sunshine delivered 72 kWh. The rest comes from the grid — but compared to the gas kiln he retired, he saves 58% energy and 100% fossil emissions. The solution is inspired by the EU project DREAM, which developed new low-emission kilns for European ceramic industry.
Avgoustinos strokes his hand over the warm metal hatch: "Solar energy gives a softer temperature curve; the glazes become deeper in tone, almost as if time laid in extra minerals."
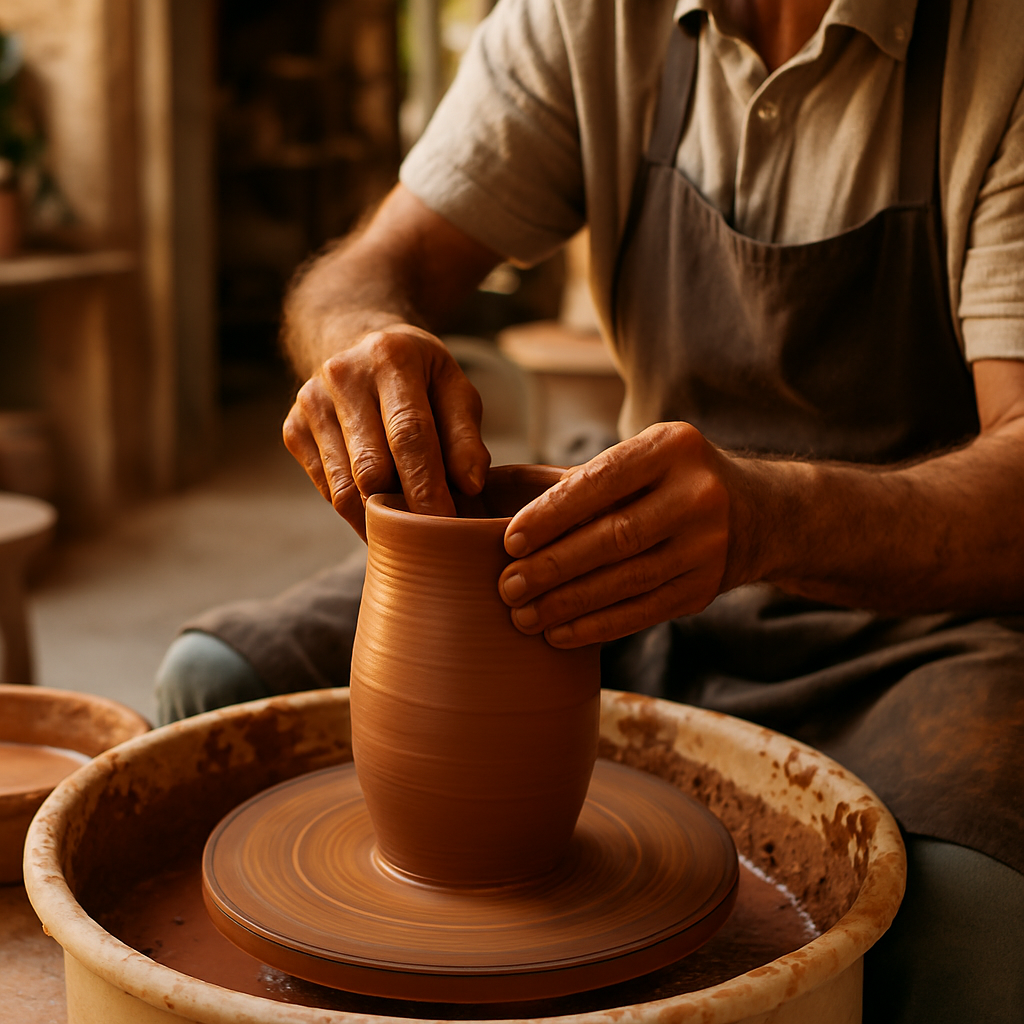
3. The pottery wheel's meditation
I get to try myself. The wheel's hum blends with cicadas' morning tempo. Clay, water, clay: high walls collapse until professional pride meets gravity's humor. Avgoustinos saves the form with two fingers. "Think about the pulse — the clay hears you," he says.
When we lift the fresh pot, he places it on the shelf for leather-hard rest. After lunch, a slip engobe made from recycled glass slip is brushed on: brown, green and cobalt blue shards ground to flour, an echo of my earlier terrazzo countertop.
4. Siesta among song and shavings
Along The Place Cyprus in the old town, more craftsmen sit hunched over pottery wheels and rolling tables. Tourists peek in, but the atmosphere is more workshop than souvenir shop — a scent of sawdust, raku clay and freshly brewed mountain tea infuses the alleys. Local school classes drop by; children get to try throwing while teachers tell how ceramic exports still reach nearly one million euros annually.
5. The glow before twilight
Waiting is part of the ritual. Around 4 PM the kiln has reached peak temperature, and we lift out test plates for reduced raku firing in sawdust boxes. Fire blazes orange, smoke smells of resin, and glazes crack in unique patterns — each bowl a fingerprint of heat and oxygen.
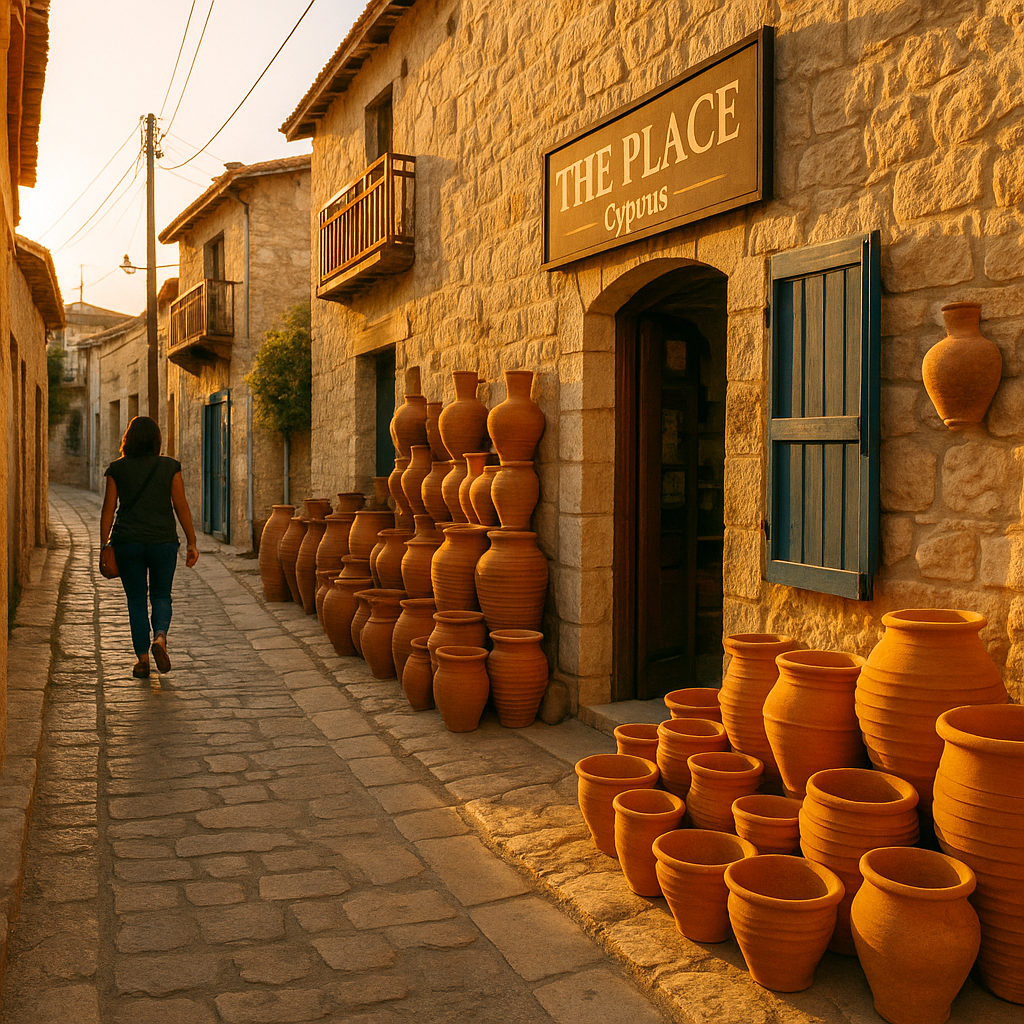
When temperature falls we open the main hatch. Twilight light breaks in the glowing vessels and casts copper-green reflections on the walls. Avgoustinos nods satisfied: "The sun painted today."
Three tips if you want to fire with sun
1. Calculate the kilowatt-hours — a 100-liter electric kiln requires ~10 kW peak power; an 8 kWp PV installation covers a normal bisque under clear Mediterranean sky.
2. Mix clays locally — Ezousa clay's iron gives warm tones but requires slow heating; mix 30% ball clay for better plasticity.
3. Visit outside high season — in February–April the pots have time to let you stay at the wheel rather than just in the shop.
Fact Box — Solar firing in Paphos
Point Data
PV installation 8 kWp on workshop roof
Energy/bisque ~80 kWh → 72 kWh solar, 8 kWh grid
Temp profile 18°C → 950°C in 11 hours
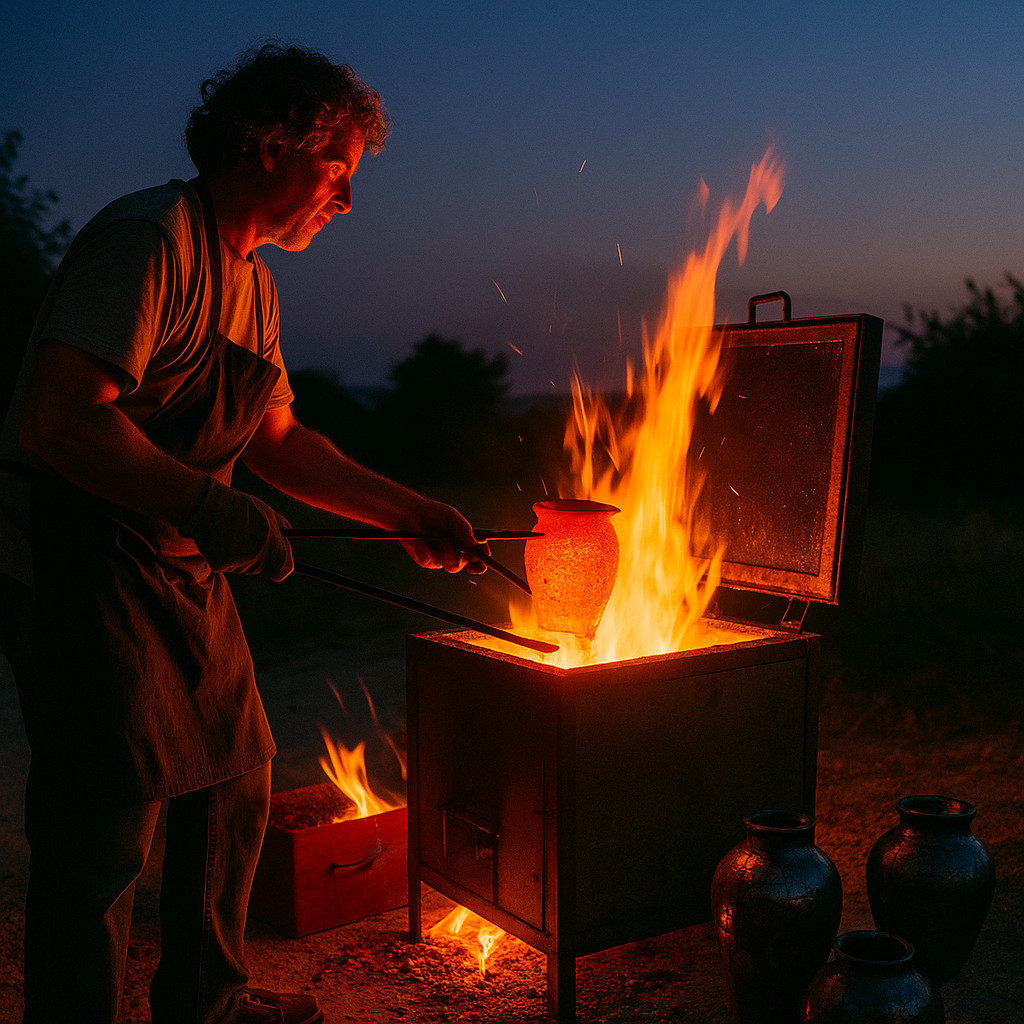
Clay source Ezousa valley alluvial clay
Visit time Mon–Fri 09–17, book wheel session 24h ahead
When I drive home via the coastal road, I still have clay in my nail beds and a still warm-glowing plate crackling in newspaper on the passenger seat. In the rearview mirror the kiln fades in twilight, but the thought burns on: it's possible to let tradition live — with sun as fuel.
Next time I follow the citrus scent into Tala groves, where agrivoltaic panels shade the fruit and feed power to the farm's cold-pressed juice press. See you among the lemon blossoms!
# Motif Alt-text ≤ 125 characters
1 Dawn clay Potter master holds reddish-brown morning clay and coffee cup in sunrise's warm glow outside workshop.
2 Solar-driven kiln Potter checks phone beside electric kiln; solar panels on roof and terracotta pots around.
3 Pottery wheel meditation Muddy hands shape tall vase on spinning wheel in sunlit, rustic workshop.
4 "The Place" in Paphos Golden street outside THE PLACE; row of terracotta pots against limestone wall while woman walks by.
5 Raku at twilight Potter lifts glowing vase from raku kiln; fire flames contrast against cool blue evening sky.
Isabelle Martens
Art historian from the Sorbonne who became a lifestyle journalist. Former contributor to Condé Nast Traveller, now a freelance writer specializing in slow luxury travel in the Mediterranean. Lives between Antwerp and Cyprus.
"Slow luxury isn't golden taps – it's having time to talk with the winemaker before buying the bottle."